Jesus Padilla stood in front of the touchpad attached to a black, steel cage and tapped in the key numbers for the box’s dimensions and what it was about to endure from the tall, robotic arm looming next to it.
Suddenly, the yellow arm whirred to life, moving in alternating combinations of sweeping grace and jerky precision. It bent down and grabbed a square pad – one that would temporarily become its sensitive hand. Using suction, it picked up the box and began to prepare to drop it repeatedly from a variety of heights.
Padilla watched as the box filled with medicine was lifted, angled at a corner, and dropped. The yellow, robotic arm then picked it up again and held it mid-air for a brief, dramatic pause as if it were asking: Are you really daring me to do this?
Before an answer could be given, the box was released – like the arm was doing a mic drop – and the cardboard corner caved slightly upon impact. The arm swooped down and picked it up again. Another brief pause. Then it dropped the box on the other corner, smashing it.
Over and over and over the robotic arm let the 42-pound box fall for a total of 102 times before it relented. Then it gingerly placed the hand-pad back on the rack and went still as a statue.
But for the box, it was just the beginning of a long series of tests to ensure it can get medicines and devices safely and intact from Amgen to medical providers and, ultimately, patients.
“If it can’t make it through here, it can’t go out there,” Padilla said.
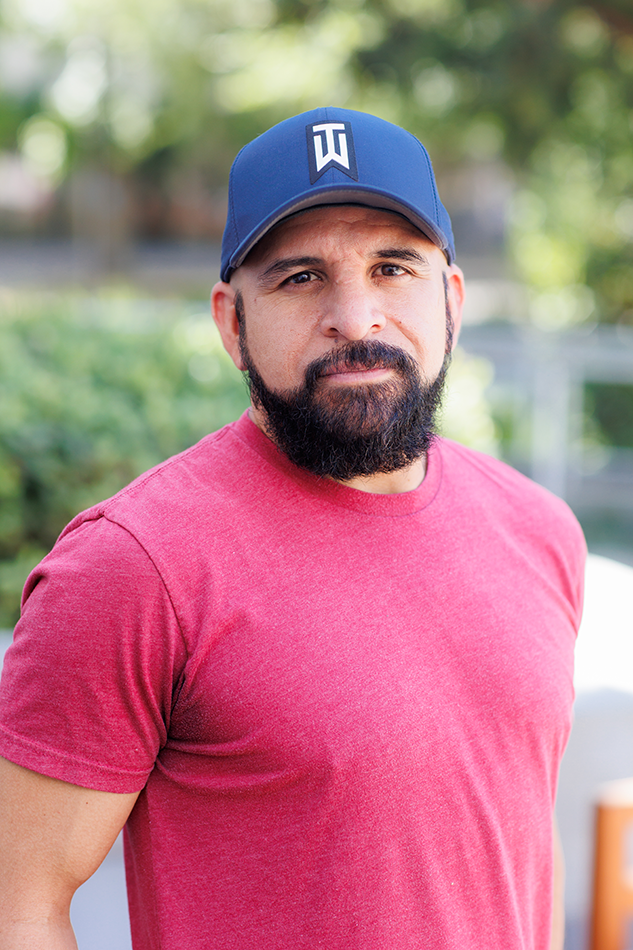
Jesus Padilla. Photo: Stacy Gleason for Amgen
Main Attraction
Regulators around the globe have specific requirements for the transportation of medicines and devices, requiring them to be able to hold at certain temperatures amid varying conditions and climates.
Padilla said each box must be able to withstand a battery of tests that simulate a variety of real-world conditions the products may experience while on a journey in the real world. The robotic arm simulates handling by shippers, loaders, delivery drivers. The drop heights are based off heights that mirror docking bays, truck beds from where the packages are moved.
The equipment in the lab is the epicenter for the rigorous process of the Transportation Simulation Test Systems – known as TSTS. Since 2014, the machines have simulated the journey products will encounter every day. Every year, the robotic arm picks up and drops about 300,000 products or boxes – which has led to it being given some colorful nicknames, including Big Bird, Megatron and Bumblebee.
Fully extended, its reach is about 15 feet. But when sedentary, it’s crouched and stands at about 10 feet high.
“Everybody and their brother wants to see it,” said Bill Lewis, a senior engineer at Amgen. “It’s definitely the main attraction.”
The TSTS lab used to operate out of Building 20 at Amgen's headquarters in Thousand Oaks, Calif., but as Amgen continued to grow and expand, Lewis said they needed a new site that could handle the volume of medicines that began coming online more than a decade ago.
The rebuild included dual chambers for the vibration and pressure testing, and by 2014, they had added the robotic arm and testing expanded to include secondary packages and devices. Before that, drop testing was done manually.
Other technological advances came as well over the years.
The compression device, which is about the size of small oven, slowly places pressure on the box as if it were in a tightening vice grip. The pressure can reach 3,500 pounds per square inch (PSI) – though it’s rare for a box to be subjected to something as heavy as, say, a compact car sitting on top of it.
And the vibration chamber, which is also where climate is simulated, has been shaking boxes for years – often simulating trucks traveling over roads at 55 mph and planes traveling at 550 mph. Over the past five years, the simulator has done more than 320,400 vibration hours by road and more than 3.5 million vibration hours simulating air travel.
“We are now basically a full-service lab that runs 24/7,” Lewis said.
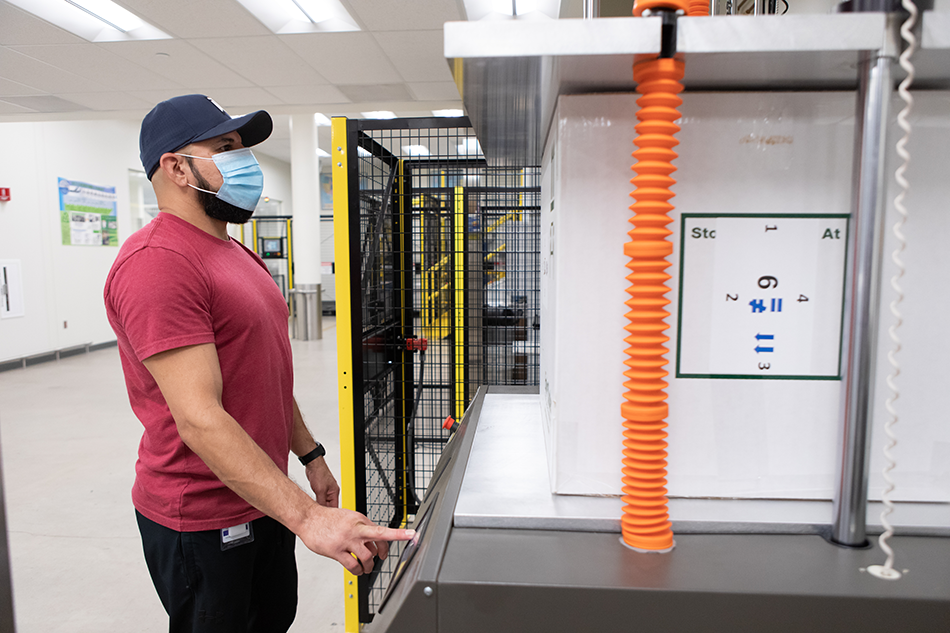
Jesus Padilla makes adjustments on the package compression tester in the lab. Photo: Stacy Gleason for Amgen
Better Quality Control
Lewis said the products that come through the lab must pass through 91.5 hours of shakes, drops, vibrations, temperature changes and pressure tests that simulate items being stacked on top of the boxes that are awaiting delivery.
But he said one change since the new lab was put in place was doing test simulations on products at various stages of development in an effort for some researchers to see how the cells might respond in those different conditions.
The process has ensured better quality control from beginning to end. He said by being able to test along the journey of the drug’s development, researchers and scientists can catch things sooner and perhaps make adjustments to medicines rather than having to wait all the way to the end to determine if it’s a pass-or-fail moment.
It’s a thorough and precise system that has continued to evolve as Amgen medicines are delivered all over the world helping people living with serious illnesses. The lab’s work is a critical step in the overall drug manufacturing process.
“It’s part of the Amgen commitment to ensure our medicines get to every patient, every time,” Padilla said. “And we are proud to be a part of that here in the testing lab.”
"Amgen Origins" is a series focused on highlighting the origin stories behind innovations large and small across Amgen.